How Data Analysis Helps Improve Qa Processes: 7 Lessons Learned
Picture this: a bustling office where data analysis is the key to unlocking the true potential of the QA process. Insights from a CEO and a Founder reveal groundbreaking strategies to enhance efficiency and effectiveness. The article kicks off with identifying inefficiencies with historical data and wraps up with improving QA with measurable results, showcasing a total of seven expert insights. This is a deep dive into the transformative power of data-driven decision-making in QA.
- Identify Inefficiencies with Historical Data
- Balance Workloads and Upgrade Equipment
- Uncover Hidden Patterns in Quality Checks
- Base Decisions on Solid Data
- Solve Problems Proactively with Data
- Optimize QA with Data-Driven Insights
- Improve QA with Measurable Results
Identify Inefficiencies with Historical Data
In a previous role, I worked closely with my team to identify inefficiencies in our QA process. Using historical data from support tickets, we noticed recurring patterns in client-reported issues, such as misconfigurations and overlooked testing scenarios. I organized this data into categories, then calculated the frequency and impact of each issue. It became clear that certain testing steps were being skipped during peak workloads, leading to predictable errors.
To address this, we introduced a priority checklist informed by the data. This checklist ensured that high-risk areas were always tested, even under tight deadlines. We also held brief team reviews after major projects to compare the outcomes against the checklist. Within three months, client-reported issues dropped by 30%. The improvement highlighted how focusing on targeted areas can make a significant difference in quality.
The experience reinforced the value of data in driving meaningful change. I learned that even simple tools like spreadsheets or ticket systems can uncover valuable insights. The key is asking the right questions of your data and staying open to making adjustments. It's not about overhauling everything but improving what matters most.
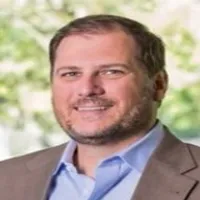
Balance Workloads and Upgrade Equipment
During my time coaching a mid-sized manufacturing company in the United States, the CEO was struggling with a high defect rate in their production line. I leveraged my background in telecommunications and my MBA specialization in finance to dive into their data. Using statistical analysis and process mapping, I identified bottlenecks and patterns that were causing inefficiencies. One critical finding was that defects spiked during shifts with lower staffing levels. Additionally, the data revealed that most defects originated from a single machine that hadn't received a maintenance upgrade in over a year. This insight was something the team had overlooked because their focus was on individual operator performance rather than equipment.
We implemented a two-pronged solution. First, I recommended adjusting staffing schedules to balance workloads across all shifts. Second, we upgraded the problematic machine and established a robust preventive maintenance plan. Within three months, the defect rate dropped by 42 percent, saving the company hundreds of thousands of dollars annually. This experience reinforced the importance of combining hard data with practical business acumen. My years of working with businesses across various industries allowed me to see the bigger picture and pinpoint issues that others might have missed. It was a prime example of how data-driven decision-making, coupled with experience, can lead to transformational results.
Uncover Hidden Patterns in Quality Checks
Data analysis uncovers hidden patterns and trends in quality checks, which might be overlooked otherwise. By examining these patterns, QA teams can identify recurring issues and work to eliminate them. This leads to a higher quality product and reduces the number of future defects.
Recognizing these trends also helps allocate resources more effectively. Engage your team in data analysis to discover these invaluable insights.
Base Decisions on Solid Data
When decisions are based on solid data instead of guesswork, the QA process becomes more reliable. Informed decisions lead to better resource allocation and efficient test case prioritization. This ensures that critical areas get the attention they need, reducing potential risks.
Data-backed decisions also enhance transparency and accountability within teams. Encourage your team to embrace data-driven decision-making for more consistent QA results.
Solve Problems Proactively with Data
Proactive problem-solving through data analysis means identifying potential issues before they become significant problems. By analyzing historical data, QA teams can predict where issues are likely to occur and prevent them in advance. This not only saves time but also reduces costs associated with late-stage defect fixes.
Early detection and resolution improve overall project timelines and quality. Start using data analysis to foresee and mitigate potential QA issues today.
Optimize QA with Data-Driven Insights
Using data-driven insights to optimize QA strategies means tailoring processes based on actionable information. This approach allows teams to refine their testing methodologies to be more precise and effective. By understanding what works and what doesn't, QA processes can be continuously refined for better performance.
This results in a more reliable final product with fewer defects. Leverage data-driven insights to perfect your QA strategy now.
Improve QA with Measurable Results
Continuous improvement through measurable results means that QA processes become better over time. By tracking key performance indicators and analyzing the results, teams can see what changes lead to improvements and which areas need further enhancement. This process of regular measurement and adjustment helps maintain high-quality standards.
It also fosters a culture of constant development and learning within the team. Implement continuous measurement strategies to keep improving QA outcomes.